Apr 30, 2020
Massachusetts companies rise to the challenge
Massachusetts companies are bringing energy, compassion and innovation to the fight versus the COVID-19 pandemic. Coverage is spotlighting a diverse sample of businesses that are contributing across various sectors. Here is the first in our series.
New Balance
Boston-based athletic footwear and apparel manufacturer New Balance has begun producing general-use face masks for health care workers, with a goal of manufacturing up to 100,000 masks per week at its Lawrence, Mass., and Norridgewock, Maine, factories by mid-April. The company worked with local medical and R&D institutions to develop a mask prototype that met FDA requirements and began production in under a week.
A New Balance spokesperson said the company is supplying the five-ply masks, made from polyurethane foam, non-woven melt blown fabric, nylon and polyester, either at cost or as a donation to local health care facilities in Massachusetts and Maine. The team is already at work designing other PPE items such as foot coverings. The company sources materials via its domestic supply chain, including companies certified to supply the medical industry.
“This initiative has kept many of our associates proudly engaged during this economic and public health crisis while our traditional retail customers are closed due to the COVID-19 pandemic.”
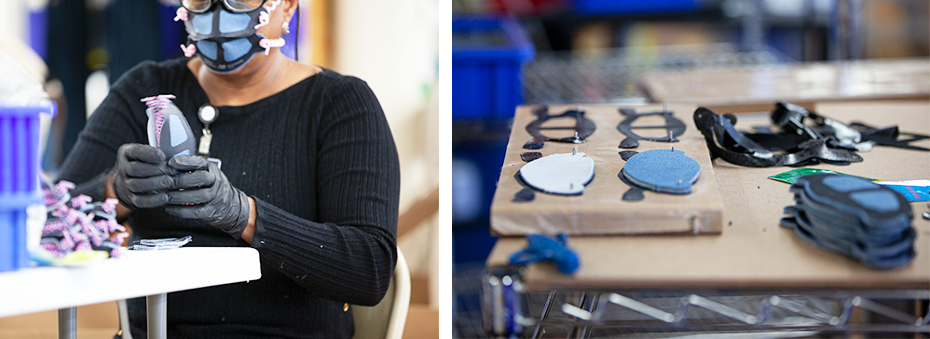
SencorpWhite
Instead of building machines that produce plastic consumer goods such as plates, trays and packs for AA batteries, Hyannis-based manufacturer SencorpWhite quickly converted existing machines to help manufacture urgently needed N95 face masks.
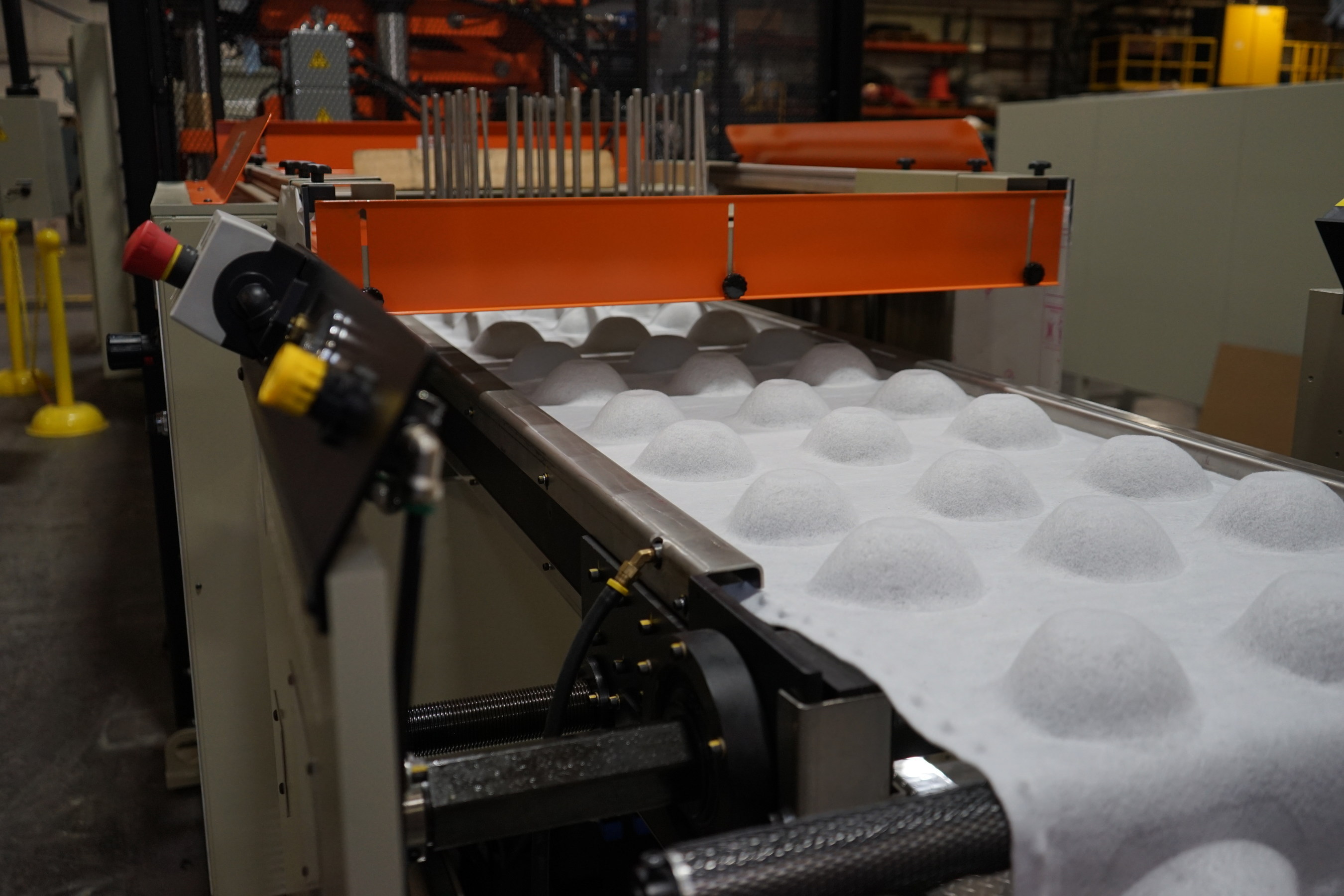
The highly skilled team worked at lightning speed to design, build and ship two machines to Honeywell in Rhode Island in less than a week. They’re currently working on a third machine with plans to build a fourth. The machines use thermoforming technology -- applying heat and then molding a material -- to mass-produce the exterior layer of the masks. Working 24/7, the machines can crank out 3 million units in a week.
“We’re on a mission to fill orders and do our part,” said Sencorp Marketing Manager Scott Boyson. “We’re lucky to be in a position to be able to help—we take a lot of pride in that.”
The company is continuing to build other machines that serve the health care industry, including those that sterilize medical devices and produce equipment for hospital pharmacies.
"It is not without its challenges, but we are here to help,” said Keith Blackwell, thermoforming supervisor at Sencorp.
“There is nothing more important than keeping our health care workers safe. They are the most important resource in this crisis."
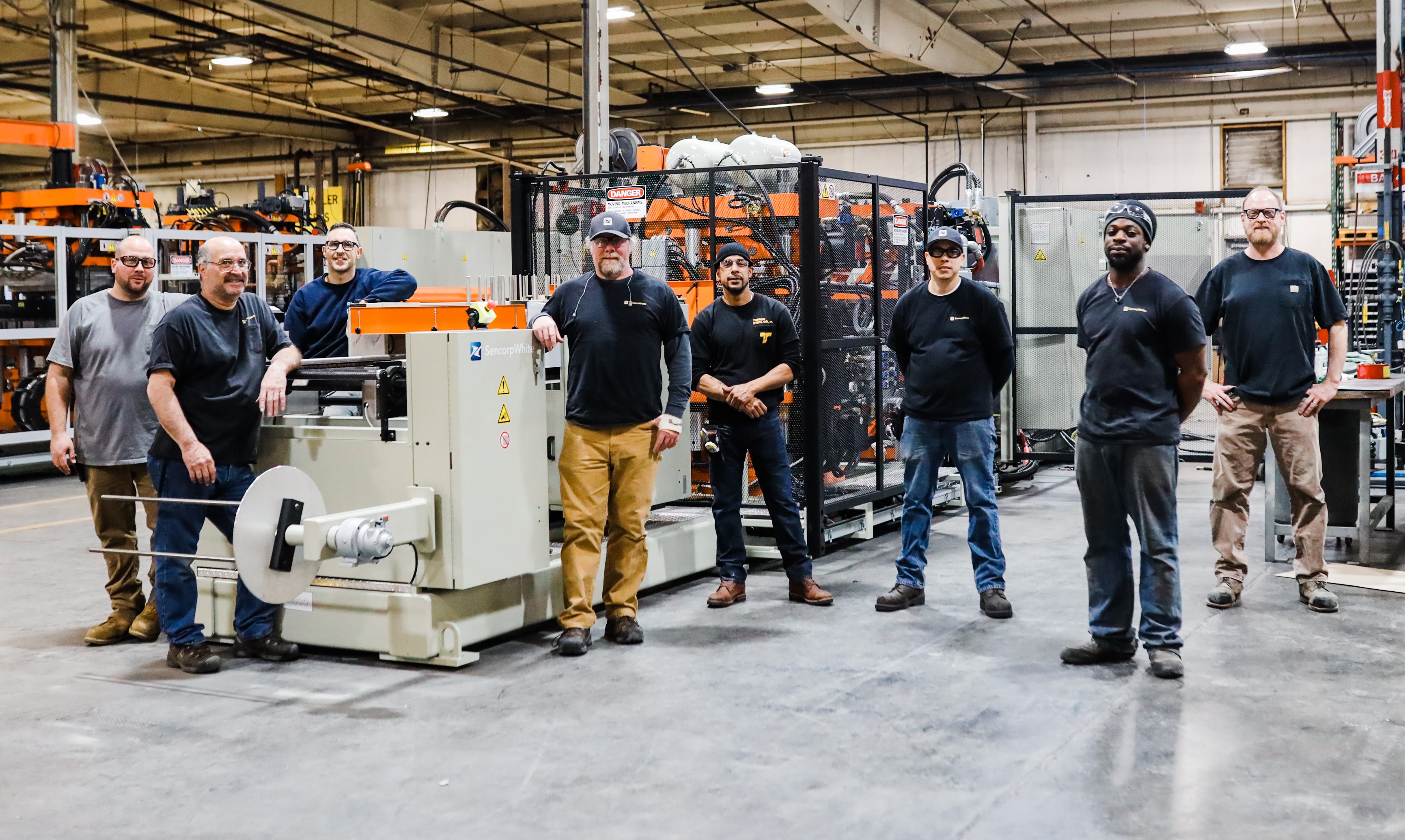
South Shore Health
With rapid tests, sanitizer and personal protective equipment in short supply, South Shore Health in Weymouth took matters into its own hands—literally. The organization’s microbiology, pharmacy and print shop teams have developed innovative “DIY” methods to conduct testing and to create hand sanitizer and face shields for colleagues.
South Shore Operations Manager Jason St. Amour took an online hand sanitizer formula from the World Health Organization and, using a blend of isopropyl alcohol, hydrogen peroxide and glycerin, he and his colleagues “mixed the concoction together in containers purchased from a national hardware chain, while using standard pharmacy compounding instruments.” The team produced hundreds of four-ounce bottles.
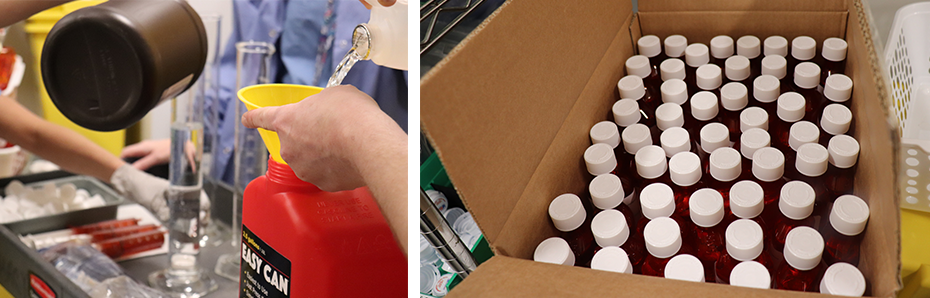
Print shop workers have also pitched in to produce face shields for colleagues. They sourced the needed materials, temporarily halted other projects and fabricated face shields for staff treating COVID-19 patients in emergency rooms, intensive care units and virus testing sites.
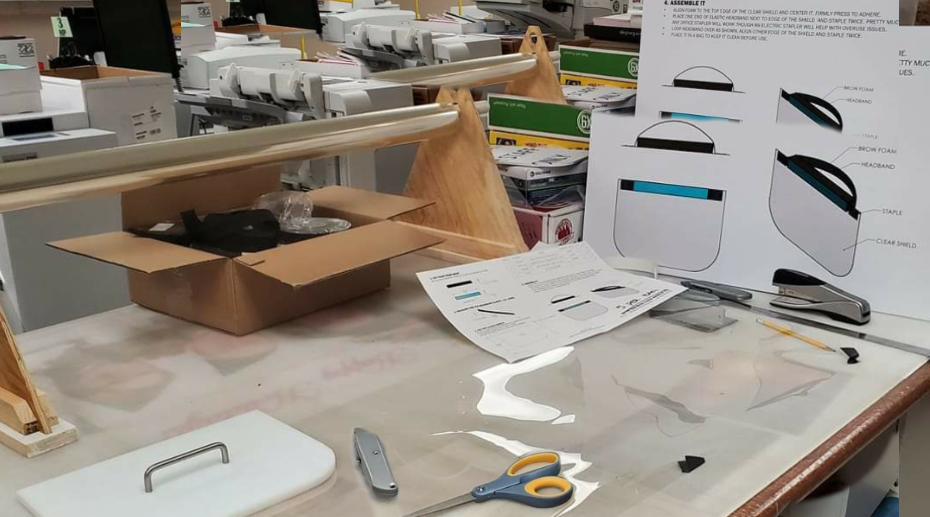
During the onset of the pandemic, South Shore Health microbiology supervisor Eve Bankert recognized an opportunity to conduct in-house testing in response to days-long waits for results from testing vendors. The microbiology expert presented her ideas to Kris Young, executive director of pharmacy, laboratory and clinical nutritional services, who gave Bankert his okay to kick the effort into high gear.
The result? Their in-house testing lab went live March 31. During just the first couple of weeks of operations, test results were returned in as little as five hours, and that turn-around time continues to decline. When patients can be discharged safely, it allows South Shore Hospital to free up beds for others who need them—which is especially critical during the surge of COVID-19 patients.
M.S. Walker
At an M.S. Walker production line in Boston, bottles meant to hold spirits and liqueurs are now being filled with hand sanitizer. The family-owned importer, distributor, bottler and national supplier of wine and spirits is providing more than 100,000 bottles of free sanitizer to first responders and other organizations in need of the product.
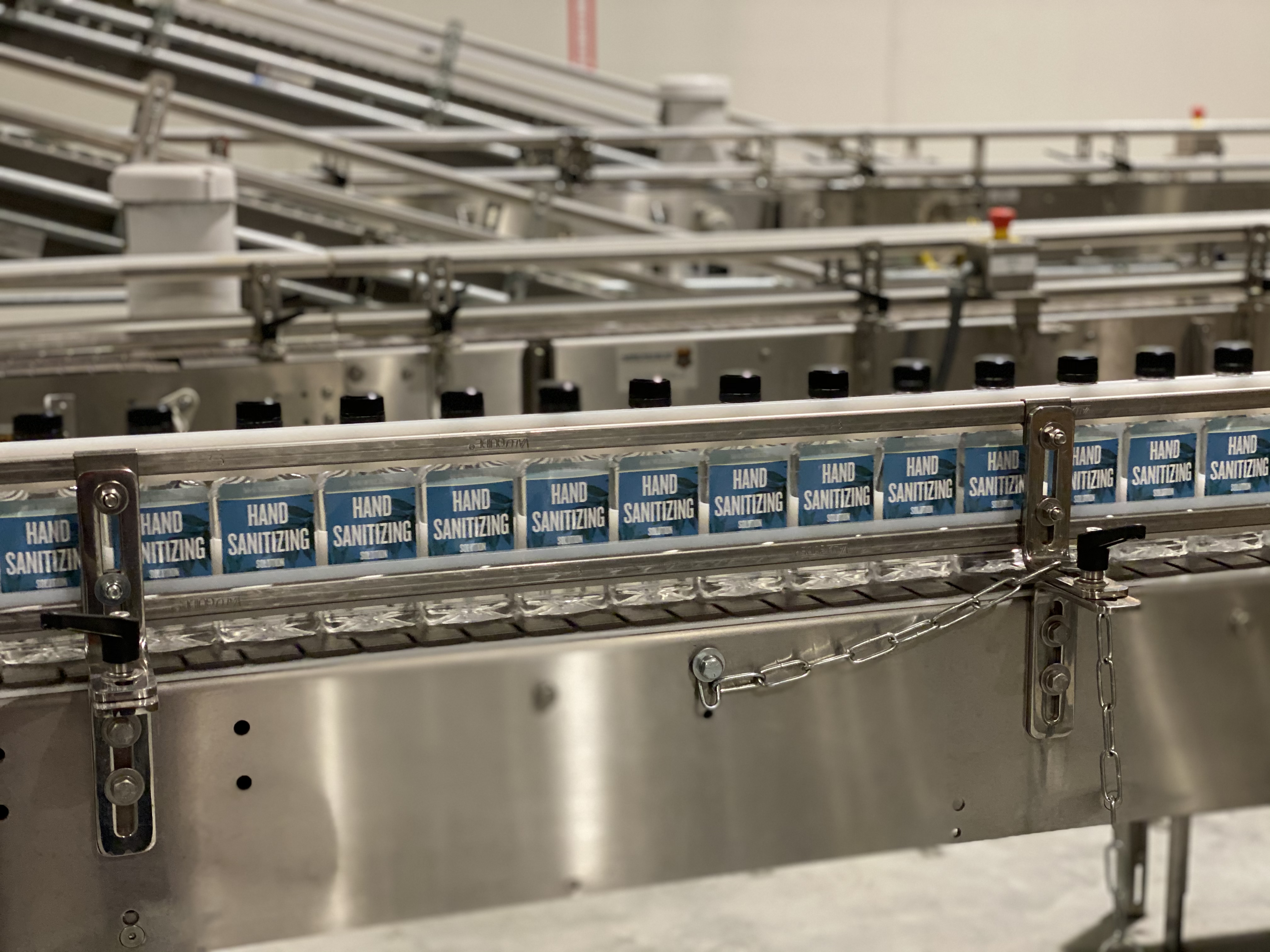
“We were able to pivot our production capabilities to sanitizer in a matter of days,” an M.S. Walker spokesperson said. “Our talented team and the quick access to ingredients that we had on hand made this process seamless and enabled us to spring into action quickly.”
The sanitizer calls for a special blend of high-proof grain alcohol, glycerin and water, in accordance with WHO guidelines.
“Apart from the overarching goal of getting sanitizer into the hands of first responders quickly, we hope that this helps others in our community to see that we are really all in this together and can help in our own little way,” M.S. Walker said.
“Whether it’s helping others in need, providing supplies or simply staying at home to prevent the spread of COVID-19, we each need to play our role.”
Did you find this article informative?
All Coverage content can be reprinted for free.
Read more here.